Checking out the Advantages of Epoxy Injection Molding for Reliable Manufacturing Processes
Epoxy shot molding stands out for its efficiency and effectiveness when you consider production procedures. This technique integrates the toughness of epoxy materials with specific production capacities, allowing you to develop complicated layouts while decreasing waste. The rapid treating times and high dimensional precision mean quicker production and lower costs. Just how does this translate into real-world applications and advantages for numerous sectors? Let's explore additionally.
Summary of Epoxy Injection Molding
Epoxy shot molding is an extremely reliable manufacturing procedure that incorporates the toughness of epoxy resins with the precision of injection molding. You'll find that this method enables the production of intricate styles and complex forms, making it suitable for various applications. By injecting warmed epoxy into a mold and mildew, you accomplish quick treating times and superb dimensional accuracy.This method not only reduces waste yet also boosts manufacturing speed, offering you the capability to meet tight due dates. You can expect constant high quality throughout batches, as each molded component keeps consistent homes. Additionally, the convenience of epoxy materials means you can customize the material homes to match particular requirements, such as thermal resistance or chemical security. On the whole, epoxy injection molding simplifies your manufacturing process while supplying premium elements that can stand up to requiring environments.
Benefits of Toughness and Stamina
When it involves durability and stamina, epoxy shot molded parts stand out in numerous applications. You'll value just how these parts can stand up to extreme conditions, making them excellent for sectors such as vehicle and aerospace. Their remarkable mechanical homes suggest they resist wear and tear better than many alternatives, ensuring a much longer life expectancy for your products.In enhancement, epoxy's resistance to chemicals, wetness, and temperature variations assures that your elements continue to be trusted even in tough environments. This longevity translates right into reduced maintenance costs and minimized downtime, permitting your manufacturing processes to run smoothly.You'll also locate that epoxy injection formed parts maintain their structural stability under anxiety, which is important for safety-critical applications. By going with epoxy, you're investing in robust solutions that can take care of the demands of your tasks, eventually causing increased consumer satisfaction and count on your brand.
Precision and Accuracy in Production
You're investing in improved dimensional resistance and regular reproducibility when you pick epoxy injection molding. This procedure assures that each component satisfies specific requirements, decreasing variations. You'll value the integrity that comes from understanding your products will certainly preserve high criteria every single time
Improved Dimensional Tolerance
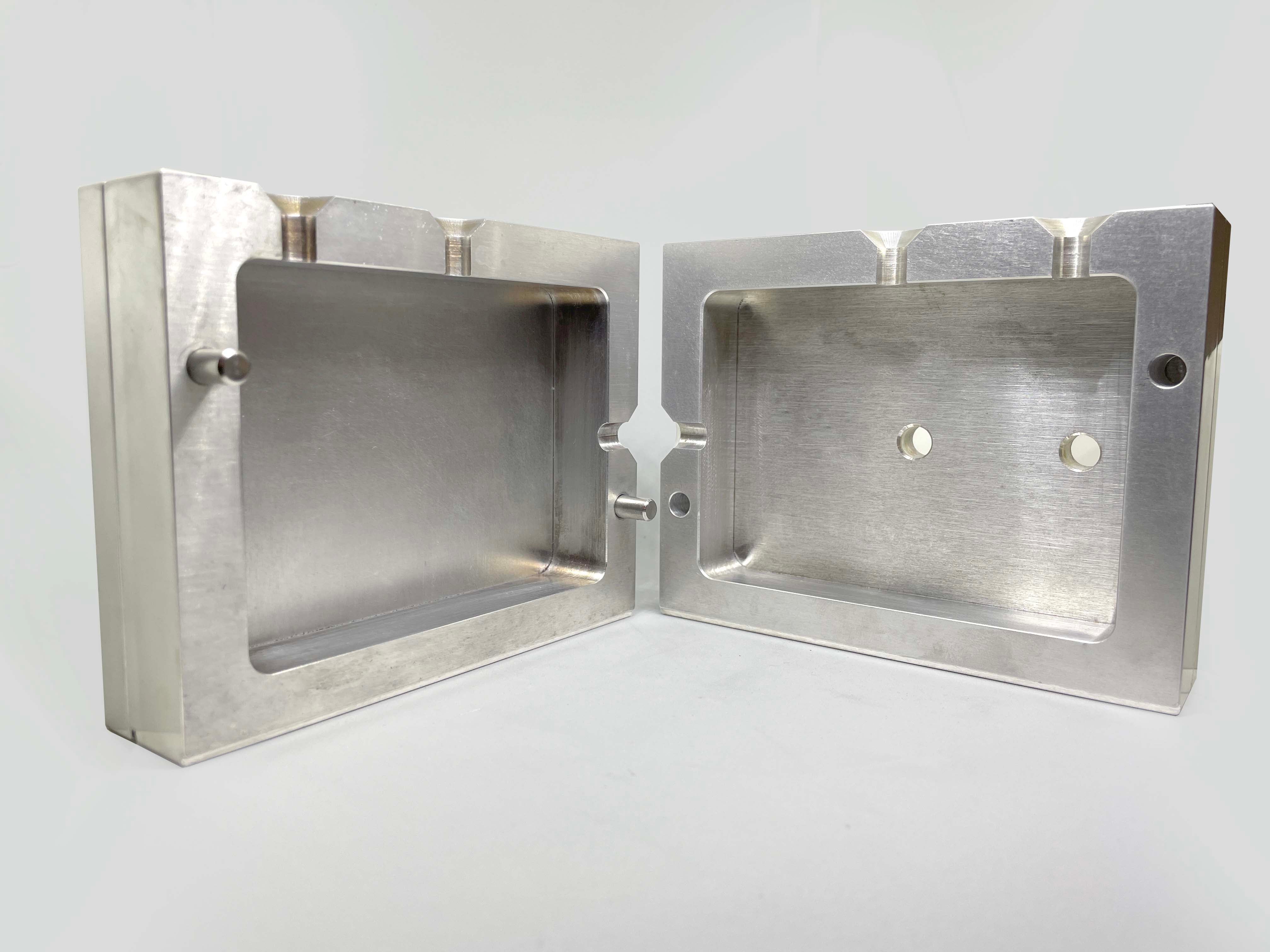
Regular Reproducibility Requirements
Uniformity in reproducibility standards is necessary for preserving accuracy and precision in manufacturing. When you use epoxy injection molding, you assure that each part you develop satisfies precise requirements every single time (epoxy injection molding). This method lowers variants, which means you will not lose time or resources on rework. You can rely on that your molds will regularly generate elements that fit completely within your assembly procedures. Furthermore, with precise control over the shot specifications, you attain uniformity throughout sets, enhancing the overall quality of your products. By sticking to constant requirements, you not just increase your production performance yet also elevate client satisfaction, knowing they'll obtain top quality and reliable items every time. Embracing these requirements can notably enhance your operational success
Reduction of Material Waste
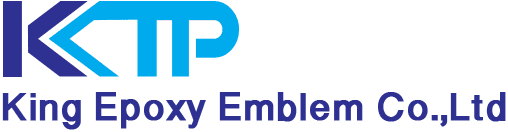
You're spending in specific product use that reduces down on waste when you pick epoxy injection molding. This method decreases scrap generation, making certain that all product matters. Plus, it enables efficient recyclable inputs, making your production procedure more sustainable.
Specific Material Use
By utilizing epoxy shot molding, you greatly decrease material waste, which not only conserves costs but also profits the environment. This procedure enables you to use specifically the correct amount of material required for each component, minimizing extra. With exact control over the shot process, you'll locate that the epoxy fills the mold perfectly, making certain that every drop matters. This precision brings about less mistakes and remodels, improving overall production efficiency. And also, by customizing the material use to your particular demands, you can optimize your supply chain and decrease stock costs. Ultimately, focusing on accurate material use assists you create top quality products while advertising sustainable techniques that add to a greener earth.
Decreased Scrap Generation
One of the key benefits of epoxy shot molding is its ability to minimize scrap generation, significantly reducing material waste in the manufacturing procedure. By precisely managing the shot of resin, you ensure that every decline counts, resulting in much less excess product. Unlike conventional approaches, where waste can accumulate promptly, epoxy injection molding focuses on reliable product use, enabling you to produce high-quality parts with very little leftovers. This not just decreases your costs yet additionally simplifies waste administration, making it much easier to preserve a cleaner office. As you embrace this method, you'll locate that lowering scrap generation adds to a much more sustainable manufacturing environment, improving your general operational efficiency. Embracing this technology implies you're taking a considerable step towards smarter producing techniques.
Reliable Recyclable Inputs
As you explore epoxy shot molding, you'll learn the facts here now find its capacity for utilizing efficient recyclable inputs, which substantially reduces material waste. This procedure allows you to incorporate recycled products, guaranteeing that you're not just cutting prices yet also contributing to sustainability. By picking epoxy formulations that consist of recycled material, you can preserve product stability while minimizing environmental effect. Furthermore, the capacity to reuse scrap created during manufacturing indicates you can redirect these products back into the process, further lowering waste. This method not just optimizes your manufacturing performance but additionally aligns with modern-day sustainability goals. You'll discover that spending in recyclable inputs boosts your operational performance, making your production processes extra cost-efficient and environmentally friendly.
Adaptability in Style and Modification
Although you might consider typical molding processes as inflexible, epoxy injection molding uses impressive versatility in layout and personalization. With this approach, you can develop complex forms and intricate geometries that satisfy specific requirements. You're not restricted to standard layouts; instead, you can tailor each item to fit your one-of-a-kind click reference needs.This versatility permits the combination of various attributes, such as undercuts and slim wall surfaces, which might be testing to attain with other methods. You can additionally conveniently customize layouts for various applications without substantial retooling, making it less complex to adjust to altering market demands.Moreover, epoxy materials can be found in a variety of surfaces and shades, giving you the creative flexibility to boost visual appeals while ensuring capability. By leveraging this adaptability, you can generate high-grade parts that stand out in affordable markets, inevitably resulting in better client fulfillment.
Cost-Effectiveness and Efficiency
When you take into consideration the costs connected with production, epoxy injection molding sticks out for its cost-effectiveness and performance. This method lowers material waste, enabling you to optimize every buck invested on resources. You'll find that the fast cycle times associated with epoxy injection molding lead to much faster manufacturing prices, enabling you to satisfy limited target dates without giving up quality.Additionally, the durability of epoxy products indicates less issues and less requirement for substitutes or repair services, even more driving down costs. With reduced maintenance requirements for mold and mildews and tools, your overall operational expenses decrease, permitting a much more streamlined manufacturing process.Investing in epoxy injection molding can lead to substantial lasting cost savings, making it a clever selection for businesses intending to optimize their production procedures. You'll not just boost your lower line but additionally boost your affordable side out there.
Applications Across Numerous Industries
Epoxy injection molding finds applications in a large array of markets, showcasing its versatility and effectiveness. In the automotive industry, you'll see it used for generating resilient components like dashboards and body components that stand up to rough problems. In the electronics industry, it's suitable for producing intricate real estates and motherboard that need high accuracy and reliability.If you're in the aerospace field, epoxy injection molding aids you produce strong and lightweight components, improving fuel performance. The medical market benefits, also, with custom-made mold and mildews for tools that demand high requirements of hygiene and safety.In building and construction, you'll locate epoxy molding used for components and installations, offering both durability and visual appeal. With its capability to adapt to different demands, epoxy injection molding verifies indispensable across these diverse sectors, making your production processes smoother news and much more effective.
Regularly Asked Concerns
How Does Epoxy Shot Molding Contrast to Typical Molding Techniques?
Epoxy injection molding supplies better precision and resilience compared to typical approaches. You'll see quicker production times and lowered product waste, making it an extra efficient selection for your production demands and improving total product quality.
What Kinds Of Epoxy Resins Are Frequently Used in Injection Molding?
You'll generally find several sorts of epoxy resins used in injection molding, including basic epoxy, fast-curing epoxy, and versatile epoxy. Each kind uses one-of-a-kind homes, dealing with certain applications and efficiency requirements in numerous sectors.
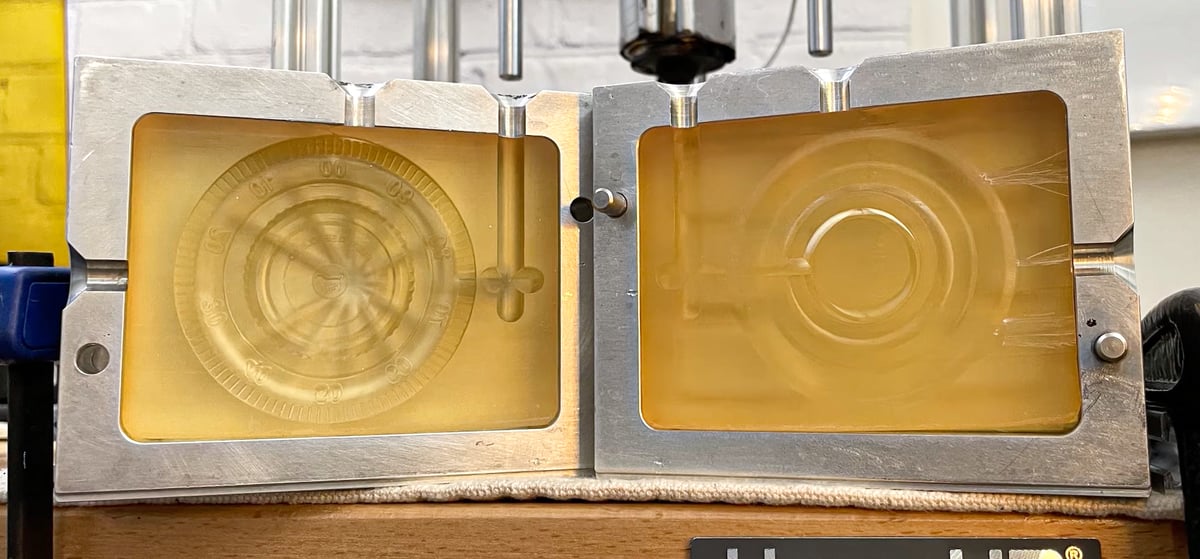
Exist Any Type Of Limitations to Epoxy Injection Molding?
Yes, there are constraints to epoxy shot molding. You may experience problems like longer curing times, greater prices compared to various other materials, and prospective brittleness in certain applications, which could affect your manufacturing performance and item longevity.
Just How Do Healing Times Affect Manufacturing Rate?

What Precaution Are Needed Throughout the Injection Molding Refine?
During the shot molding process, you should put on protective equipment, guarantee appropriate air flow, maintain devices consistently, and follow safety and security methods. These procedures aid protect against crashes, injuries, and guarantee a secure workplace for every person included. Epoxy injection molding is an extremely reliable production process that combines the strength of epoxy materials with the accuracy of injection molding. One of the vital benefits of epoxy shot molding is its capacity to reduce scrap generation, markedly reducing product waste in the production process. You might believe of conventional molding procedures as rigid, epoxy injection molding offers amazing flexibility in design and customization. You'll find that the fast cycle times connected with epoxy injection molding lead to quicker production prices, enabling you to meet limited target dates without compromising quality.Additionally, the durability of epoxy products implies less defects and much less demand for substitutes or repair work, better driving down expenses. You'll generally find several types of epoxy materials made use of in injection molding, consisting of standard epoxy, fast-curing epoxy, and flexible epoxy.